| Design Principles & Consultation |
| Studio Consultation |
Tuesday 9am - 1pm & Thursday 2pm - 6pm
Week 1
COMBINED TUESDAY LESSON
For the first lesson, it was a combined lesson on Tuesday. We were tasked to prepare a presentation on what we were planning to do for our studio project this semester. We had to establish the direction we wished to take for our project and if there were any design refinements we wish to take. It was a more casual presentation to get us back into the flow of things . At the end of the presentation, we were asked to create a schedule for us to plan out what we needed to do for this entire semester for this project. After making the schedule, we had to show it to our lecturer.
Evaluation of Previous Design
What needs to be improved?
-
Overall better construction of the slipper
--> Folding issues
--> Crease issues
-->Exposed edges and sewing flaws
-
Logo needs to be more legible
-
Better CMF, colour variants
-
Better packaging
-
More dynamic renders and real life comparison shot
​
What to do?
-
Better understanding of manufacturing processes and material
-
Reevaluate fabric choices and have a more broader selection to choose from
-
More research on colour schemes (Conduct Survey during testing phase)
-
Better Packaging (Must it be adraw string bag) and create tags & card maybe
-
Logo design (Think of the way it will look on product)
-
More testing on washability
Compeititors
-
What is special about my own product?
-
How can I surprise my target market?
-
How do I get people to know that they fold it?
Interview Questions
​
Manufacturing process
What are the steps/ manufacturing processes that are needed to produce a pair of hotel slippers?
How long does it take you to produce one? / How many slippers can you produce a day?
What are the materials that are most frequently used for hotel slippers? How much of each material is used?
Where do you get your material from?
How much do the materials typically cost?
​
Hotel's concerns and priorities
What are the main priorities that hotels have in regard to the production of hotel slippers?
Typically, what is the price range that hotels are willing to pay for their productions?
How many hotel slippers are produced for each hotel on average?
Have there been cases of hotels wanting to go green with their hotel slippers?
If so, what were the challenges? / What would be the challenges of having more eco-friendly hotel slippers?
Schedule​
This is the draft of the schedule I have plan for my semester
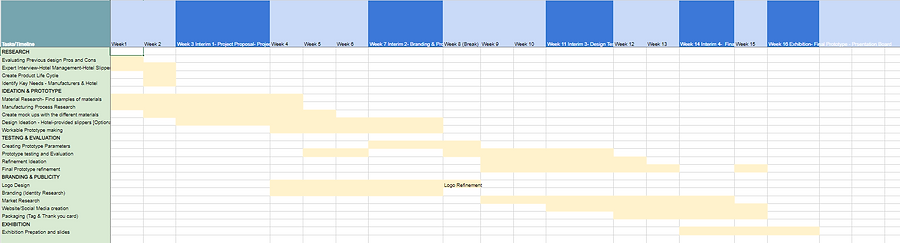
Week 2
TUESDAY LESSON
During this lesson we wer
THURSDAY LESSON
During this lesson, we were introduced to the first mini-project that we had to do. We had to make a presentation board advertising some children's toys that Siwei had brought. They were her son's bathroom toys. we were grouped into teams of 2 to 3 and we had to make 2 A3 presentation boards. I was grouped with Jan for this project. We divided the task up to Jan doing the 2D illustration while I did the photos and 3D CAD model. As we discuss and do our project, Siwei also went around to ask about our progress with our project and check our schedule




STUDIO PROJECT
Interview Answers
​
What company do you work for?
I am working with a hotel amenities and accessories supplies company based in Singapore. The company supplying bath amenities such as shampoo, shower gel and accessories such as dental kits, vanity kits and hotel slippers across the world. Singapore is the Asia Pacific head officer and with HQ in Canada and subsidiaries in Mainland China, Europe and Middle East. The company working with various OEM factory in China for slipper’ production.
Company Name: Hunter Amenities International.
How long have you been working at this company?
I been working with this company for 9 years.
​
What is your job scope at the company?
I am the Brands, products and Customer Service Manager for Asia Pacific.
​
What are the steps/ manufacturing processes that are needed to produce a pair of hotel slippers?
Step 1 - Hotel’ specification requirement, such as design, material and cost.
Step 2 – Sourcing for raw materials & making sample for hotel approval.
Step 3 – Upon confirmation of sample and materials.
a)Cutting of slipper sole, subject to size. In most cased will be using EVA materials.
** Ensure left and right foot portion.
b)Cutting of upper cover material, such as velvet, cotton, non-woven material.
c)Printing, embossing, or sewing the hotel logo on the upper cover portion, subject to hotel spec.
d)Sewing the upper cover.
e)Sewing/combining both upper and sole portion of the materials.
f)QC check before packaging
g)Packaging – put a pair of slippers into client’ chosen material such as plastic bag, non-woven bag or paper bag.
h)To pack slippers into big carton box for export/for delivery. Usually will be 100pairs per carton. The weight of the whole big carton will be restricted to <12-13kg. This is to work safety and staff wellness.
Step 4 – Arrange logistics for export or delivery.
​
How long does it take you to produce one? / How many slippers can you produce a day?
In most cases, slippers can be produced within 7 day, subject to quantity and available of raw materials. Each team/department will follow
The main OEM factory we are working with is based in Suzhou, China. This factory can produce 100k pairs per day.
​
What are the materials that are most frequently used for hotel slippers? How much of each material is used?
For sole – it will be Ethylene-Vinyl Acetate (EVA) sole. This is rubber like material and with anti-slip cutting. This is soft to wear.
-Cheap sole will be using paper cardboard.
For upper – imitation cut velvet materials (most popular). This is made from knitted fabric from cotton and polyester resampled.
-Non-woven fabric (cheaper). This this cheaper version of slipper with cardboard as sole.
Where do you get your material from?
The factory are getting raw material locally in China. Hotel’ accessories materials are widely available in Jiangsu, China.
How much do the materials typically cost?
This is subject to market condition. The supply been limited since 3 years ago due to pandemic and the cost been increasing. The current situation are consider stable and the cost are still 30% higher than pre-pandamic period (before year 2019). A tropical cost for standard hotel slipper, 28cm, velvet with 1cm EVA sole will be SG$0.40 (ex-works factory cost, exclude shipping cost, import duties anc etc from China to Singapore)
​
What are the main priorities that hotels have in regard to the production of hotel slippers?
Quality and cost.
Typically, what is the price range that hotels are willing to pay for their productions?
For hotels in Singapore
4-5 stars – SGD$1.20 – 1.80
3 stars – SGD$0.80 - $0.99
​
How many hotel slippers are produced for each hotel on average?
A typical 300 rooms hotel consumption for slippers per month is estimate at 6,000-8,000 pairs per months.
​
Have there been cases of hotels wanting to go green with their hotel slippers?
Yes, Hotel are now looking into ‘Go Green’ initiative. Such as exploring to bamboo material slippers and etc. The first step is to eliminate the individual plastic packaging.
​
If so, what were the challenges? / What would be the challenges of having more eco-friendly hotel slippers?
Such as eliminate the individual plastic packaging been cause hotel operation issue such as hotel guest feedback on un-hygiene. Without the individual plastic packaging may also cause the slipper easy to get wet during transportation.
Another main factor is the cost of the eco-friendly material. The cost been very high and may double-up hotel’ operation cost and this may lead to increase in hotel’ room rate per night.
Material research (+ cost)
​
Fabric (Breathable, thinner, non slip)
-
Corduroy Fabric
-
Pile Fabric
-
Cotton Knit fabric
-
Terry Clothes
​
Cushioning
-
Memory Foam (S$1.46 per mm)
-
Lux Foam
-
Polyurethane Foam
​
Need high tear strength to survive washing
Either the sole is harder or the foam is memory foam like
Need to come up with a way to ensure the back of the shoe doesn't flap
Sole
-
Silicone (Shore A Hardness 40°-50°)
-
Rubber
Design refinements
​
Revisiting old concepts, specifically my sock concept. this is to solve my flopping slipper issue by giving it a backing like a footsie. Silicon backing
Week 3
COMBINED THURSDAY LESSON
So for this lesson, we had our presentation on our current progress with our project. Overall, it was good research done and allow me to better solidify my project. In the end of this research, I decided to not pursue a hotel-provided option due to the cost.
Thing to do​
-
More material research (identify
-
More Sketches & Mock up
-
Narrow down fabric choices & sew sample
-
Wash test
-
Silicone sole making
-
Decide what I need to test with travellers
Thing to make​
-
Sample of material
-
Wash Test
-
Silicone Mold (wood and vinyl)
-
Footsie with silicone sole inside ---> Silicone is inside though :(
-
Shoe with pattern like a footsie
-
Experimenting with different thickness of Eva foam and urethane foam
-
Range of Prototype--> 1-3 type
-
Make a guide for my aunt
Week 4
TUESDAY LESSON
Lesson on
THURSDAY LESSON
Today's lesson we went through our 2 presentation boards of


STUDIO PROJECT
MARKET RESEARCH
​
-
Millenial travel the most, then Gen Z
-
Online advertisement & Social Media to book and research
-
82% of milenials travels
-
58% of millennials are Solo travellers
-
embracing the YOLO lifestyle
-
Young and free
-
Online advertisement
-
purpose and fulfilment
-
70% of millennials would rather spend money on experiences than things.
-
Jet setters
​
Fabric Choices​
-
stretch Cotton & Polyester blend
-
Polyester (Different type)
-
stretch velvet (Polyester & spandex blend) ---> For the top
-
Interlock Jersey
​
Prototype Construction​​

​
​
-
“Millennials reject anything that feels like corporate marketing and they've pushed us all in how we guide our brand experience.”
-
personalisation and connectivity
-
With millennials, don’t try to be cool. Be vulnerable and authentic
-
Experience, transparency, social, frictional experience
-
builds being socially conscious into all aspects of life
-
The Millennials are the first generation born after the technological revolution. The world feels smaller to them than previous generations and they are intimately connected to one other—regardless of geography
​

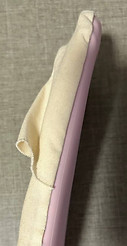
Week 5
TUESDAY LESSON
This week class was online and we went through some videos on different designers. Also, some of us did our presentation on our designer that day.
THURSDAY LESSON
This week class was online and so we had a briefing about our next mini-project. We had to make mood boards on the CMF trends of different furnishing. I was teamed with Sung and Anna. We were assigned to do hard furnishing. I was tasked with doing bathroom and living room. After that, Siwei did one on one consultation with each of us
STUDIO PROJECT
Fabric Choices​​
​

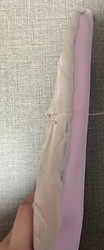
Prototypes & Sketches​
Trying out layer
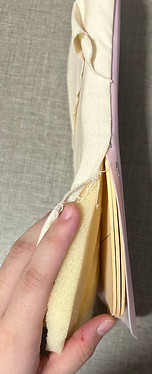


Making Silicone
Week 6
TUESDAY LESSON
This week I presented my designer, Hella Jongerius. Hella Jongerius was a designer that I had stumbled on while researching for this presentation and I kind of resonated with her research as she was someone who is involves herself heavily in colours and materials. This was what the current stage in my project was and I was curious about where her dedication to the research comes from. I think I learn a lot about how I should grow as a designer from her especially since I was honestly hitting a roadblock on my project and where I desire to continue to grow as a designer.

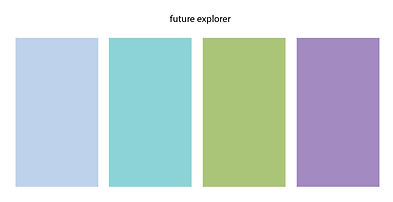
After the presentation, we were given a task to do about colour. We were grouped into teams of 2 to 3. We were given a theme and we had to come up with a colour palette for each of the themes given. I was grouped with Kim for this project. The first theme that was given was "Joyful Energy".
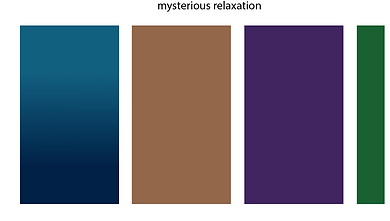
THURSDAY LESSON
For this Thursday's class, we went through the CMF trends mood board we created. For myself, I decided to focus on the bathroom area and the dining room area. Overall I think, I think that my presentation board were done up quite well. Particularly the first one on the Statement Vanity. I think I was able to highlight key trends in bathroom interior design for the vanity space, from the brass details to the marble and the type of finishing. I think that the layout of the CMF board is also one that I took a lot of time to position and I am happy with the information conveyed through it. I think I could have included a statement about the curved edges but I think my layout was a bit too cramped already. But I do think that the second mood board wasn't as well done as I may have spent too much time on the first. I was also worrying that I would encroach on my other teammates' CMF board as I wasn't completely sure where they were headed with theirs. I think I should have looked into the type of shape that dining tables contained and be keener in spotting different textures and finishing like ratton.

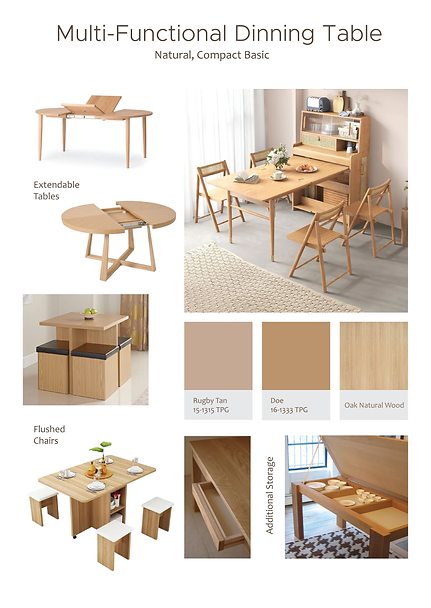
STUDIO PROJECT
Making Silicone
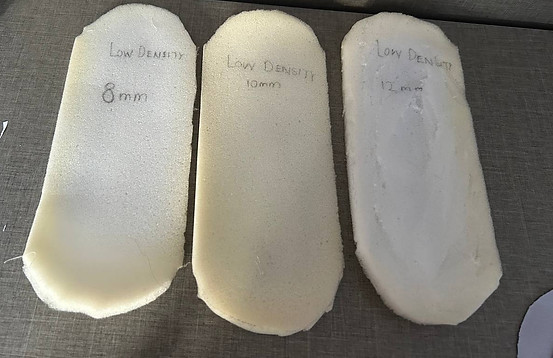
Testing out Thickness of Layers
Trend Research and Mood Board
​
Bedroom Trends
-
Calming colour palettes - mindfulness and considered consumption
-
Checks and stripes (Maybe?)
-
Warm, Earthy Tones and Colors - warm clay and coral, darker shades of amber and plum
-
Peace and Harmony in the Space - Modern organic colors and textures
Compeititors
Mood Board Name
Week 7
TUESDAY LESSON
For this week's lesson, we went to the Kvadrat showroom for a visit at 2pm. They are a

COMBINED THURSDAY LESSON
Unfortunately, I was having MC that day and I couldn't present my project. These are the presentation boards I have prepared as well as the sample that have been done.


Week 9
TUESDAY LESSON
I consulted with Chun Beng on the progress of my A1 Presentation Board and he gave me some feedback on it. Overall the poster layout was all right, but he suggested some helpful ways to display some of the information, such as the write-up and target users. He also said that I should use the more extended version of my "How to use" journey map as it showed a deeper understanding of its use journey. For the second page, The picture of the layers displayed was noted to be rather unrefined and it was suggested that I displayed it differently.
​
From there, we also discussed about my prototype and the issue with my prototyping skill with the silicone making the piece too heavy to use. So we did do some discussion on how to refine the model to prevent it from flopping. And later in the week, I did do a refinement in the prototype.
​
After that he suggested that I also add some washing symbols to better showcase my products' selling points. Finally, he got me to relook at my logo and got me to refine it some more by ensuring my font thickness was consistent for all.
STUDIO PROJECT
Prototypes
Logo Refinements
COMBINED THURSDAY LESSON


Unfortunately, I was having MC that day and I couldn't present my project. These are the presentation boards I have prepared as well as the sample that have been done.
Week 10
For the rest of the weeks, were all focused on our studio project. Hence from here on out I will just be showing you my studio project progress and the feedback given to them, unless there is a presentation.
STUDIO PROJECT
Fabric top
Making Shoe Sole
(Silicone/3D Print)
Logo Refinements
Week 11
STUDIO PROJECT
Fabric top
Making Shoe Sole
(Silicone/3D Print)
Overall Construction
Logo Refinements
Week 12
STUDIO PROJECT
Scouting location for filming video
COMBINED THURSDAY LESSON
We had our final interim presentation before our exhibition. Overall, this was a simple update check to see where my progress was at. Was given some suggestions on the dart size and location and overall construction.
Week 13
STUDIO PROJECT
Refining sewing fabric tops
Making final 3D printing file to print
Sole bottom design
Logo Design
Week 14
TUESDAY CLASS
We had short lesson on materials and manufacturing processes. Chun Beng had gotten us to watch some videos on manufacturing processes last week and we were given a quiz to do. I guess I did rather well in it since I got second place, but it is properly because I am very familiar with the content since I was taught it previously.
STUDIO PROJECT
Final logo refinements
Tag Designs
Construction of both top & bottom
Week 15
STUDIO PROJECT
Figuring out Construction
Final tag refinements
Final Construction
Making of Bag
Week 16
Final Submission & Exhibit
Final Model
Final Logo
Poster
Making of Bag